Speed Skating: The age of made-to-measure boots?
If in the old days, made-to-measure speed skating boots were reserved to elite skaters. Today, these products are the object of a growing demand from more and more skaters. You do not have to be a world champion to treat yourself to high range gear. We paid a visit to Philippe Renard who explained us how these performance gems are madeâŠ
Par alfathor
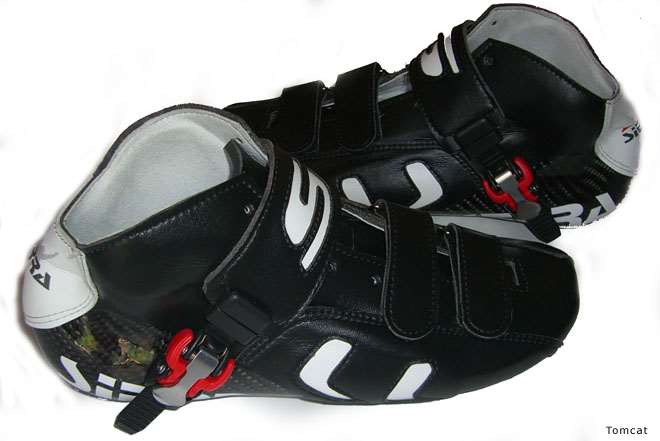
A handful of boot makers
Numerous concepts improving the boots’ comfort
In the world of skating, the concept of auto-molding or thermoformable boots saw the light in the middle of the 90’s in speed skating, street skating and aggressive skating.
That process is used by all the big brands. On the other hand, no maker offers a real customized boot. From artisanal making to standardized manufactured production, the margin is still considerable. With the arrival of laser foot printing, a manufactured production of made-to-measure boots may be eventually possible.
Made-to-measure skates: a handful of makers for a niche market
Only a few specialized makers share the market of high range made-to-measure boots. They essentially work in Italy and Australia but there are also a few ones in France. Philippe Renard is one of them. That former elite skater and national winner of the French Inline Cup progressively improved his products these last years. He has become a reference in the market.
Today, his products equip skaters such as Sébastien Henri and Nicolas Duval…
Prices and delivery periods of made-to-measure makers
In order to make a pair of made-to-measure boots, at least two months are needed between the moment of the molding of the foot and the final product. It is not due to the speed of the maker so to speak, but to some incompressible time factors for the drying.
Steps
- making of the « negative » molding of the foot, which will need time to dry,
- then making of its « positive » print — that operation will take at least one week,
- adding of the different layers of carbon which will have to solidify little by little. Here again, weeks go by…
- last but not least, the leather upper is added to the boot.
According to the makers, times are not the same: they can vary from 2 to 4 months, even more. When a shoe is made in Italy or Australia, you will have to take into account the time of transport too.
On the market, prices are between 500 and 1.100 € according to the makers. When asked why they do not wish to produce at a bigger scale, the answer is clear: a large production irremediably leads to less quality.
Make me a carbon boot…
1) The molding is a crucial moment
The making starts with the printing of the foot thanks to plaster strips, often identical to those used in hospitals for casts. The maker progressively wraps up the foot with the damp strips. After a few minutes the whole mold has solidified. You get a « negative » print of the skater’s feet. The foot is freed with an incision on the upper part of the cast.
Once the mold taken off, it is immediately closed back and sent to dry. Later, a « positive » mold will be created by injection into the « negative » mold to get the shape of the skater’s foot. All the maker has to do left is to use that print as the basis of the boot structure.
2) The setting up of the blocks
Once the positive mold of the foot has dried, the blocks which will enable to set up the frame will be put with spacings of 165, 190 or 195 mm according to the type of frame.
3) The boot
Once the blocks put, the actual work on the boot may start. Progressively, layers of materials are going to be closely adjusted on the structure. The maker will use glass fiber, carbon fiber, kevlar or aramid according to the client’s rigidity or comfort demands…
The combination of those materials confers its properties to the skate. In choosing one or the other, you change the boot’s characteristics. Carbon is chosen for its rigidity, glass fiber for its elasticity, aramid and kevlar for their resistance.
Once the successive layers adjusted and dry, the boot is at a raw state and still needs to be sanded and varnished to get its bright and smooth radiance. Here again, drying time is needed.
4) The upper part
Once the boot finished, comes the turn of the upper part (which is not the sole). It may be made of natural leather or Lorica. Natural leather is generally more comfortable but deteriorates more easily. Regular maintenance needed. Lorica is a synthetic material that is close to leather. It is waterproof, breathing and often has an antibacterial treatment.
The upper part is made of several parts
5) Finishing…which are put together on the boot. The whole has to be glued and the cutting perfected.
The boot is almost finished. The last step is the adding of the tightening system, which may vary according to the demand: micrometric buckle, laces, strap… and that’s it!
Advantages and drawbacks of molded boots
Theoretically, the boot perfectly fits the shape of your foot. Thus no more loose feet and welcome precision! You consequently gain in power and have more possibilities on effective run-ups.
Made-to-measure molding may be interesting for people whose foot shape is specific (flat or hollow foot…) Today, makers even adapt their products to include orthopedic soles. If that is your case, you should yet see a chiropodist before venturing into made-to-measure boots.
On the other hand, the boot being so close to the foot, wearing socks might become quite problematical. Most professionals skate bare foot.
A few tips
As mentioned above, a few shops make molds which they send to the other end of the planet. The result is not systematically up to the skater’s expectancies and recourses are complicated. It is a specific competence with a specific knowledge. It is thus recommended to favor proximity with the maker.
Photo gallery
Useful links
The manufacturing of a pair of roller skates
Manufacturing of composite frames
The trade secrets of skate boots
The manufacturing processes of skate frames
How are made rink-hockey skates?
Anatomy of a pair of Quad Skates
Translation: Chloé Seyres
Photos: Alfathor