The manufacturing of composite frames
Composite frames with carbon are far from being all over the market for the moment, but they may take more and more shares to aluminum frames in the future. EO Skates had the kindness to explain us the different manufacturing processes of those futuristic models...
Par alfathor
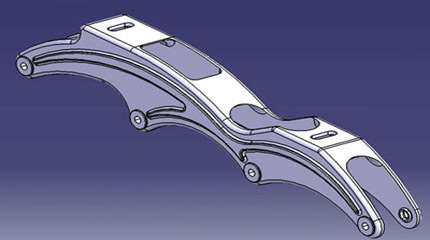
Composite frames
The frames made of composite materials are frequently used for mid-range models on the market. For example you find various models mixing nylon and glass fiber.
On the other hand, in high-range products, until now, aluminum was ruling, offering a good compromise as for weight, solidity and rigidity.
Making of the models
As we saw it in the previous articles, the making of composite frames, made of carbon and foam, requires a design phase.
The aim is to get the right handling in ensuring a constant resistance. Thus the design and choice of the carbon fiber (thread of the material, weight per square meter, orientation of the fibers, etc.) determine the performance of the frame.
There are three types of ‘carbon’ frames on the market today:
– The hybride frames (carbon sides assembled with aluminum parts): That process requires very little investment, as only the sides of the frame are made of carbon. They are just directly cut out of carbon panels. The assembling being mechanical, it considerably reduces the benefits of the carbon material, being limited to the length of the frame. The transmission of energy between the boot and the frame is thus less favorable.
– The ‘full’ monocoque frames: they are made from a series of layers of carbon constituting the whole width of the frame. That solution avoids all mechanical assembling, but does not enable the variety of models without multiplicating the tools. Moreover, that monocoque technique makes quite a heavy product in the end and does not exploit the whole potential of carbon.
– The ‘composite’ monocoque frames (the sandwich technique) are inspired from a well-tried technique used in aeronautical, aerospace and formula 1 manufacturings, for its performances as for rigidity, handling and weight. Today only one manufacturer in the world uses that tehcnique: EO Skates, the French designer and manufacturer.
Close-up on EO Skates
Their current frame, the DIABLO .4, is made of several layers of carbon wrapping a foam of low density on the sides.
To that sandwich technique is added a carbon cover on the side, on the whole length of the frame, ensuring rigidity and handling.
That technique requires specific and expensive tools for each of the stages of the process:
- Cutting of the carbon material
- Cutting of the foams
- Making of the frame
- Making of the carbon cover
- Drilling and sticking of the insets
The making of a frame requires a long and meticulous preparation. Several hours are needed to make one. Add to it the different possibilities of decorations (stickers and paint).
Each model of frame requires its own set of tools and its own time of implementation, which explains the cost of that ‘made-to-measure’ technique.
Another manufacturing process?
The SENTOUNO Belotti frames would be made of an aluminum structure covered with a carbon material, the carbon cover probably aiming at rigidifying the whole. We do not have more information on that manufacturing process for the moment.
A few questions to the founders of EO Skates
We have interviewed Eric and Fred, the designers of the EO Skates frames.
What are the main differences between the composite frames?
Brands like TNT use a relatively simple solution, without any specific tool. The aluminum parts are machined, the carbon sides are cut and then the whole is assembled. It’s handy, we have a standard for all the models, for the boot fixing or for the axles rigidifying the frame. A complete range is available without having to invest into multiple tools.
On the other hand, a product that is assembled doesn’t offer the same performances as monocoque frames (aluminum, carbon or composite). The energy of the skater isn’t transmitted totally through the frame.
Moreover, full carbon has a far lower rigidity-weight ratio than foam carbon composite.
The sandwich structure results from the assembling by sticking of two thin layers on a lighter core that will hold the space (see diagram above). In separating those two layers, you considerably increase the flexing performances.
It is an asset of the models of your brand?
The strength of EO also comes from the shape. The outside wave-shape is not only for the aesthetics, it also serves as a reinforcement. A carbon rod is used to reinforce the whole structure. Its shape enables to gain in rigidity and torsion.
How did you come to create the company?
I started skating in 2000 and I quickly came to speed skating.
At first, we did our own frames ourselves in our garage because we didn’t find what we were looking for on the market. Our different experiences led us to use different materials. After several dozens of prototypes and a few disappointments (laughs), our investigations on composite materials and carbon were a revelation!
Our garage quickly became inadequate for the making of our frames. We then decided to take the plunge in creating our own company. We invested on our personal funds to start. Today, it is several dozens of thousands of euros to arrive where we’re at.
How do you sell your products?
We have decided to do direct sales because our production costs are exorbitant (5 to 6 times the price of an aluminum frame).
In going through distributors then shops, the frames would end up at 800 or 900€ the pair!
Despite all that, we have been contacted by a few French and American retailers. I take the opportunity to thank the Rollertech. Loops racing and Teknosport for their support too.
The different titles won with our DIABLO .4 (French Championships and Cup, Grand Prix of Bourgogne) and the authorization of the 110 mm encourage us to make a 110 mm model. The problem remains the investment and the number of skaters likely to buy them (don’t hesitate to let us know on our website!) Our current model is already suitable for 104 mm wheels, which is an excellent compromise in-between the 100 and 110mm.
What are the strong points and the weak points of the composite-based frames, especially at EO Skates’?
Handiness and rigidity: Aluminum has an elasticity modulus of 75.000 Mpa against 240.000 Mpa for carbon.
Lightness: the DIABLO .4 (2007) weights 130g. The 2008 version will be heavier in order to gain in handiness. We have also reinforced the front and back parts.
Reactivity: Aluminum is a deformable material, contrary to carbon which always goes back to its initial shape. Last but not least, carbon renders energy very well, it acts like a bow, getting slightly out of shape and sending back the energy.
Are the risks of breakage higher than with composite frames?
The advantage of aluminum frames is that they rarely break, but they lose their shape, wear out and become less performant.
There is no transition for carbon, when the stress exceeds its properties, it breaks.
In which conditions does it break?
Carbon only breaks in case of important shocks. When it breaks, aluminum has been out of shape for a while.
- Blue: elastic deformation
- Green: plastic deformation
- Red: break
And what about vibrations?
Opinions are divided, some people find a great comfort of rolling and others find it too rigid.
When your bearings are worn out and have a lot of playing, it resonates like the frame or the carbon wheels of a road bike.
What is your target?
All the speed skaters. The youngest will find an advantage in the weight. The national and elite skaters will of course benefit from the weight on long distances but also and above all from their handiness and their reactivity, which will take on their full meaning during sprints.
It’s a product without compromises, you aim at the very-high end of the range.
Is it small production volumes then?
The manufacturing time is considerable.
There are 8 parts on our main mold. A skilled labour is required to make them. The preparation and manufacturing times are very long. You can’t multiply the tools either, the investments are heavy. You can’t change models the way you like, it’s a big drawback. Just like all the products using that technology, the series are small, it remains restricted productions.
In order to draw a parallel with cycling: a high-end carbon frame is almost 100 hours of work for a purchase price of 4.000 or 5.000€.
As for the decoration, engraving is delicate. We can put stickers, silkscreen printing, paint, or do tampography (stamp).
Eric: what is your initial training?
I have a technical training: conception of industrial products. I designed a lot of plastic parts for cars. I spent more than a year on the design of the expansion of the Parisian airport (CDG), especially for its metal structure. I underwent training on simulation-based calculation. Everything about the analysis by finite element in static and dynamic planes.
Illustration: frame by Hopiframe
The models on the market
Belotti Sentouno Carbon
Brand: Belotti
Model: Sentouno Carbon
Year: 2007
Size: 12’60 (320 mm), 12’80 (325 mm) or 13’00 (330 mm)
Wheels: 4×100 mm
Axle distance: 165 mm
Composition: 7106 double hollow aluminium covered with carbon
Price: 250€
Hopiframes
Brand: Hopiframes
Model: 4×100
Year: 2007
Size standard type A: 12’00 (305 mm) or 12’52 (318 mm) or 13’1 (333 mm)
Size type B « 1K Fine Weave » : 12’52 (318 mm) or 13’1 (333 mm)
Wheels: 4×100 mm
Axle distance: 190 or 195 mm
Composition: Aluminum bridges and carbon frame
Price: 299 $ USD
EO Skates Diablo .4
Brand: EO Skates
Model: Diablo .4
Year: 2007
Weight: 125 g
Size: 12’80 (326 mm)
Front bridge: 97 mm
Wheels: 4×104 mm max
Axle distance: 195 mm
Composition: Carbon
Price: 319 €
TNT 5MC 1004
Brand: TNT Corea
Model: 5MC 1004 (A or B)
Year: 2007
Weight: 190 g
Size: 12’80 (325 mm)
Wheels: 4×100 mm
Front bridge: 94 mm
Back bridge: 105 mm
Axle distance: 195 mm
Composition: 7075 T7 anodized aluminum and carbon
Prix : NA
Photo gallery
![]() |
![]() |
![]() |
![]() |
![]() |
![]() |
Links
EO Skates
Hopiframes
TNT Corea
Photos: EO Skates and Alfathor
Translation: Chloé Seyres