The manufacturing of a pair of roller skates
Apart from a few pairs of made-to-measure speed skates, most skates are made with similar manufacturing and designing techniques: Studies on the needs of the skaters, creation in design committees, making of prototypes, tests, and mass production. Focus on the different stages...
Par alfathor
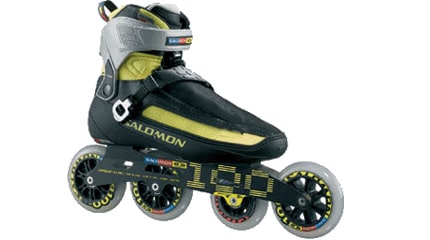
The making of a pair of skates
![]() |
![]() |
First of all, the industry of inline skates has not actually innovated in its manufacturing processes. Most of them already existed: injection (used for skis and for plastic materials in general), extrusion (used in metalworking industry) or computer aided designing (CAD with 3D design softwares…) Skating does not represent the same financial issues than the car industry. The brands have thus limited their investments.
Then, over the course of the years, the manufacturers have patented their processes : it is the case of K2 with the Softboot or that of the process of bi-injection for wheels. Between 1980 and 2000, the brands registered a considerable number of patents related to skating. The tendency has slowed down for a few years with the concentration of the market.
There was a time when K2 and Salomon were engaged in a merciless legal war as for the semi-soft boots concept.
Design in committee
The designing of an inline skate is the same as that of lots of sports products; it starts with the drawing of the product and ends in the designing of a prototype, then leads to various tests enabling to evaluate the conformance of the product to the specifications set by the manufacturer.
Manual and CAD designing of the skate
The first designing stage is manual. The manufacturers are very concerned about aesthetics, as inline skates are products addressed to young people and would not put up with any lack of taste. The diversification of the various types of practices requires that each model has its own characteristics and properties which would be easily identifiable by the skaters, making it different from the other skates.
It is then refined on graphics palette for two months (for the Rollerblade company). CAD Softwares enable to design each part separatly from the others. Their dimensions are rigorously calculated.
Then, technical solutions are brought to create the propositions of the designers. At the world’s number 1 manufacturer’s, Faustino Luchetta supervised the designing. In 1998 he explained on a French TV channel that the technology used to create a skate depended on the type of skate, giving the example of the all-terrain skate Coyote.
The making of the prototypes
The complete information is then sent to machines which start immediately the cutting or the injection of the parts. A skate is made in a few hours and is then subjected to tests.
Testing the prototypes
The tests are made in order to determine if the skate meets the specifications of the manufacturer. The skate is tested by experienced skaters who subject it to the worst constraints and detect what the machines cannot: flexibility, support, comfort…
Meanwhile, some machines can simulate the life cycle of an inline skate fast-forward (flexibility, bending tests…)
All the parts are tested: resistance of the wheels to abrasion on 50 km, life expectancy of the ball bearings…
If the skate meets the specifications wanted, it will be then mass produced.
Click on the part you want to know about its manufacturing stages.
![]() |
![]() ![]() |
![]() ![]() ![]() ![]() ![]() ![]() ![]() ![]() |
![]() ![]() |
Links
The manufacturing processes of skate frames
Anatomy of an inline skate boot
How are made rink-hockey skates?
Speed Skating: The age of made-to-measure boots?
The trade secrets of skate boots
Translation: Chloé Seyres
Photos: all rights reserved