Los procesos de fabricación de los platinos
El chasis o el platino es la piedra angular de nuestros patines. Su forma, su longitud y su rigidez varía con la disciplina y las necesidades de los patinadores. Compuesto o poliuretano, son moldeados o inyectados, tales como las botas. De aluminio, pueden ser embutidos, extrudidos o talladas. ¿Cuáles son las diferencias entre estos procesos?
Par Vernon SULLIVAN
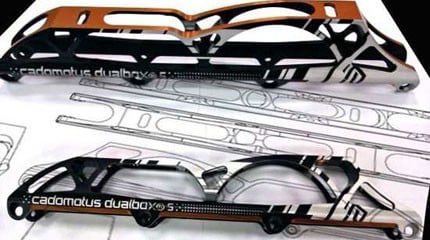
La concepción de los platinos.
Los platinos compuestos
No nos detendremos mucho en la fabricación de placas de plástico y compuesto porque haremos un artículo completo sobre este tema
Los platinos en metal
Naturalmente, como por todos los chasis moldeados, los platinos de metal también son desarrollados y diseñados por CAD (Computer Aided Design).
El software avanzado incluso les permite pasar las pruebas de resistencia al momento de la concepción. El diseñador y el ingeniero pueden definir y establecer si desean reducir o aumentar el espesor de la pared, añadir un puente, o la eliminación de material en un lugar u otro.
El chasis puede ser: extrudido, embutido o tallado en la masa según el uso que le vamos a dar, el precio que estamos dispuesto a poner y cualidades que estamos buscando.
La primera dificultad en el concepto de un platino es optimizar con éxito tanto la masa, la fuerza, la rigidez y la altura especialmente desde la llegada de gran diámetro de ruedas tipos 90, 100, o 110 mm y más.
El embutido, método poco costoso
El embutido es una técnica de fabricación sencilla es pasar una hoja de aluminio u otro metal con el espesor deseado en una prensa. El material se deforma a la forma deseada.
En general, ambas superficies de un platino se realizan por separado. Son ensamblados con una parte central en la que se fijan las dos « laminas ».
Este proceso se utiliza en la mayoría de los platinos de gama media. En realidad, es menos costoso que la extrusión. El fabricante pierde menos material, no tiene que roscar el platino para acomodar ejes simples, a diferencia de los modelos extrudidos. Por leso, los costes de producción se reducen.
Las platinos embutidos tienen mejor desempeño que los platinos compuesto de nylon y fibra de vidrio, por ejemplo, pero muestran limitados en comparación con los modelos extrudidos mucho más rígidos.
Fabricación de platino extrudido
El proceso de extrusión es simple: un bloque de aluminio es presurizado y forzado a través de un troquel. Así obtienes un perfil que tiene volver a trabajar para conseguir la forma deseada por el fabricante.
Esta técnica ofrece una buena rigidez a los platinos.
Posteriormente, a menudo son anodizados para aumentar la resistencia a la corrosión. Es posible decorar las placas, cambiando el color de baños de anodización. Los estándares utilizados suelen ser los de la Aeronáutica (Aluminio 6000, 7000…).
El tope: Los platinos cortados en la masa
Un chasis tallado en la masa es en alguna manera « esculpido » en un trozo de aluminio. Aquí entramos en producciones en pequeñas series y más bien en la alta gama.
El material es tan rígido que tendría que tener una prensa de una fuerza considerable para doblarlo. Este proceso de fabricación permite cosas imposibles de hacer con un perfil clásico. Pocos fabricantes utilizan este proceso de fabricación casi artesanal. En Francia, son los platinos Diabolik que se realizan por este método.
Los acabados de los chasis de aluminio es extremadamente minucioso. Todo se hace por la máquina numérica. Los cortes de los platinos son refinados al láser. Se tarda unos diez operaciones para completar un platino de aluminio.
Las marcas entonces tienen que poner serigrafía sobre los platinos: o sea por anodización, como lo vimos antes o añadiendo una sencilla capa de pintura.
![]() |
![]() |
enlaces utiles
Mantenimiento de los chasis o platinos de patines
Fotos : www.diabolik-skating.com