La fabrication des roues de roller, visite chez RollX
On se plaint souvent qu'elles sont chères, s'usent vite, glissent, collent trop, on vante leur roulage, leur rebond, leur réactivité. Pas de doute, nos roulettes sont souvent au coeur des conversations entre patineurs ! Rien de telle qu'une visite chez notre fabricant de roue français RollX pour en apprendre un peu plus sur la manière dont elles sont réalisées...
Par alfathor
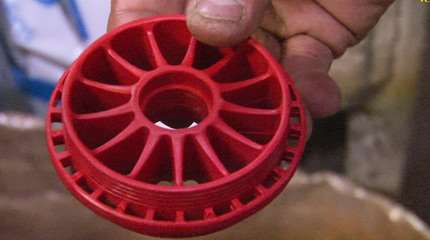
Article de décembre 2010 remis à jour, jetez un oeil aux vidéos en lien tout en bas !
Elles n’auront bientôt plus de secrets pour vous
Nous avons profité d’un déplacement dans le Doubs pour faire une halte à Chézery, dans l’Ain, non loin d’Oyonnax. Le petit village de 400 habitants abrite l’unique fabricant français de roues de roller, RollX. L’entreprise familiale créée voilà plusieurs dizaines d’années par Alain Myallonnier a su se faire une place sur le marché français parmi les géants que sont Matter ou MPC. C’est Olivier, le fils d’Alain qui nous fait la visite…
La conception
Les grandes marques conçoivent leurs roues sur ordinateur, en CAO (Conception Assistée par Ordinateur). Le développement prend souvent plusieurs années.
La réalisation des moules
On part d’un bloc d’acier que l’on va usiner pour lui donner la forme d’un moule. Ce moule sera le négatif de la pièce. Les moules sont réalisés en usinage traditionnel (tournage).
L’empreinte de la jante, quant à elle, va se faire en électro-érosion (pour schématiser, le procédé inverse de la soudure, on enlève de la matière). Ce procédé est indispensable pour creuser la matière des moules qui sont traités et donc très durs. On utilise ces matériaux car ils vont pouvoir résister à plusieurs millions d’utilisations.
En fait, on va d’abord concevoir une électrode de cuivre qui aura la forme du noyau de roue. Une sorte de « positif ». C’est elle qui va creuser le bloc de matière (le « négatif ») à la forme souhaitée. Elle va descendre très lentement dans le bloc d’acier vierge. Un arc électrique apparaît entre les deux pièces et va creuser la matière. Pour 12 mm de profondeur, il faut compter une quarantaine d’heures de traitement.
La conception d’un moule représente plusieurs centaines d’heures de travail et des prix pouvant varier entre 5.000 et 40.000 Euros selon la complexité de la roue.
La fabrication des noyaux
Une fois que l’on a réalisé les empreintes de moules, elles vont partir à l’atelier d’injection et être posées dans les corps de moule de la machine qui va effectuer les injections à la chaine. On change seulement l’empreinte rapportée dans la machine pour faire tel ou tel diamètre de jante.
Un noyau, c’est avant tout de la matière première. Selon l’usage de la roue, on trouvera différents matériaux : des polymères, de la fibre de verre…
La matière première se présente sous forme de granulés. Ils sont colorés (blanc, jaune, rouges) pour avoir différentes couleurs de noyaux. Pour faire du rouge par exemple, il suffit d’avoir 2% de grains rouges au milieu de 98% de grains blancs pour avoir la couleur demandée.
On mélange deux matières : une rigide et une plus souple pour avoir à la fois du roulage et une bonne résistance à la casse.
Avant d’être envoyés dans la machine, les granulés de matière sont passés dans un dessiccateur, une machine qui va les sécher. Enlever l’humidité va éviter que les noyaux cassent à l’usage.
Dans la machine, la matière est chauffée à 230/240°C. Une vis envoie la matière dans le moule régulé en température. Un cycle de production dure plus de 2 minutes. La matière est injectée par un tout petit trou à 2200 bars. Pour conserver l’étanchéité, la machine exerce une pression de 50 tonnes de fermeture.
Ensuite, la pièce est éjectée et séparée de sa carotte (résidu du canal d’injection), une fois qu’elle a suffisamment refroidi.
A la sortie de la machine, les dimensions de la pièce ne sont pas encore bonnes car la chaleur a dilaté les matériaux. Il faudra attendre environ 1h pour que le noyau de la roue ait la forme parfaite.
Concevoir un noyau, nécessite un savant dosage des différentes matières selon les propriétés que l’on souhaite privilégier : relance, souplesse, solidité…
Les premiers noyaux vont donc partir en test dans des laboratoires spécialisés en plasturgie à Oyonnax afin de tester leurs propriétés. C’est une étape indispensable et très coûteuse également.
Avant de mouler les sur-noyaux sur les jantes, on va chauffer les noyaux entre 80°C et 100°C. La température doit être égale à celle au moment du surmoulage pour avoir une meilleure cohésion de la gomme sur le noyau.
Le moulage des sur-noyaux
Il existe 2 procédés pour la fabrication des sur-noyaux : l’injection et le surmoulage. Chez RollX, c’est la seconde qui est privilégiée et sur laquelle nous allons nous pencher…
Tout d’abord, on doit régler la machine qui fait le mélange des matières composant le polyuréthane. La différence de dureté s’obtient en modifiant les quantités des 3 produits de base. C’est aussi le moment où l’on peut ajouter le colorant de la roue. La matière se présente sous forme de granulés, comme pour le noyau de la roue. Les composants sont alors mélangés et fondus.
Les moules des sur-noyaux sont comme de petites cuves ouvertes au sommet et qui se ferment par le haut. Après les avoir bien nettoyés, on y dépose le noyau qui va recevoir la gomme. Il est indispensable que le moule soit parfaitement propre, la moindre saleté engendrant une imperfection sur la surface de la gomme. On nettoie donc les moules entre chaque série de moulage.
Les moules sont tout d’abord chauffés à une température de 80 à 100°C suivant la matière utilisée. Ensuite on place la jante au milieu du moule avant de le refermer. Vient la phase de remplissage. On fait couler la matière chauffée encore liquide dans les différents moules.
Au bout de quelques minutes, la matière va se figer et l’on va pouvoir démouler la roue.
A ce stade de la production, la roue est loin d’avoir atteint sa dureté définitive. Quelques minutes après être sortie des moules, une roue peut avoir une dureté de 60A alors qu’elle aura au bout du compte une dureté de 85A après séchage.
Le moulage a engendré un excédent de matière à la périphérie de la roue. Il va donc falloir s’en débarrasser. Qu’à cela ne tienne, un coup de machine et on découpe ce surplus.
On va ensuite les laisser sécher durant 24 heures avant de les repasser au four pendant 12 à 72 heures selon la matière.
Il faudra 1 à 2 mois de repos avant de pouvoir les utiliser, le temps que la polymérisation s’achève et que la structure chimique de la roue se stabilise.
La finition
Les roues bien séchées vont être nettoyées avant d’être imprimées puis emballées.
L’impression des motifs de décoration sur les roues se fait par tampographie. On utilise un cliché en tôle gravé en creux très fin sur lequel on va déposer de l’encre. Le tampon reste dans la partie en creux, le tampon descend dessus et va ensuite se poser sur la roue pour l’imprimer.
A chaque couleur, il est nécessaire de changer le cliché. Pour 3 couleurs, on change 3 fois de cliché pour l’impression sur une seule et même roue.
L’emballage
Vient enfin l’ultime étape, l’emballage ! On aligne les roues sur un axe pour les glisser dans un film plastique qui sera chauffé afin de bien tenir l’ensemble. Bien évidemment, on oublie pas l’autocollant de la marque ainsi que l’étiquette sur laquelle figure les informations techniques sur la roue.
Merci RollX pour cette visite très instructive !
Les 4 vidéos de la visite chez RollX
Etape 1 : La fabrication des moules
Etape 2 : la fabrication des jantes
Etape 3 : le moulage du surnoyau
Etape 4 : finitions et emballage
Liens utiles
- Les innovations technologiques récentes des roues de roller
- La fabrication des roues de roller
- Physique de la roue de roller en ligne
- Roues RollX : quel modèle pour quel usage ?
- Roues : la course au diamètre s’arrêtera-t-elle ?
- L’entretien des roues
- Site de Rollx
Photos : Alfathor
Merci à RollX pour l’accueil
Grounk
26 octobre 2010 at 12 h 23 minC'est vraiment une petite équipe super motivée qui sa
f-wtss
26 octobre 2010 at 12 h 12 minBravo à Roll'X pour son savoir faire et son remarquablement sympathique accueil de l'équipe de REL.
On comprend mieux l'enthousiasme de ceux qui ont attrapé le "virus" Roll'X.
Et on se dit aussi que le matériel de fabrication et tout le travail effectué sur une roue justifient un prix qui semble finalement assez "ajusté"!
Buclaloup
26 octobre 2010 at 11 h 32 minarthur
26 octobre 2010 at 11 h 27 min