Les procédés de fabrication des platines de roller en métal
Le châssis ou platine est une pièce maîtresse de nos rollers. Sa forme, sa longueur et sa rigidité varient en fonction de la discipline concernée et des besoins des patineurs. En composite ou en polyuréthane, elles sont moulées ou injectées, comme les coques. En aluminium, elles peuvent être embouties, extrudées ou taillées dans la masse. Quelles sont les différences entre ces procédés de fabrication ?
Par Vernon SULLIVAN
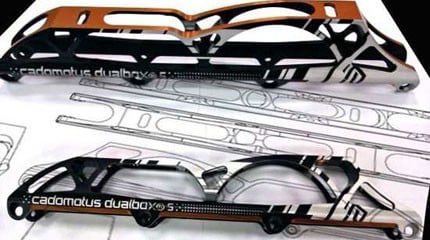
La conception et la fabrication des platines de roller
Quel que soit le mode de fabrication, les châssis ou platines en métal sont développées et dessinées par C.A.O. (Conception Assistée par Ordinateur).
Des logiciels évolués permettent même de leur faire passer des tests de forces lors de la conception. Le designer et l’ingénieur peuvent ainsi définir ensemble s’il faut réduire ou augmenter l’épaisseur d’une paroi, ajouter un pont, enlever de la matière à un endroit ou à un autre.
La première difficulté dans la conception d’une platine est de réussir à optimiser à la fois la masse, la résistance, la rigidité et la hauteur surtout depuis l’arrivée des roues de grand diamètre.
La fabrication des platines roller en composite
Nous n’allons pas nous appesantir très longtemps sur la fabrication des platines en matière plastique et en composite car un article complet est à votre disposition en suivant le lien ci-dessous.
Lire l’article sur la fabrication des platines composites
Il existent diffrents procédés industriels pour fabriquer des châssis de roller en métal
Les châssis peuvent être :
- extrudés
- emboutis
- moulés
- taillés dans la masse (usinés)
La méthode choisie sera différente selon le coût que l’on veut investir dans la production mais aussi selon les caractéristiques techniques que l’on recherche. Il est possible de combiner deux méthodes de fabrication, comme une phase d’extrusion avant une phase d’usinage, ou une phase de moulage avant une phase d’usinage.
L’emboutissage : une méthode peu coûteuse pour des produits d’entrée de gamme
L’emboutissage, c’est quoi ?
Il s’agit d’une technique de fabrication simple qui consiste à passer une feuille d’aluminium ou d’un autre métal de l’épaisseur désirée sous une presse qui exerce une pression de plusieurs tonnes. Le matériau est déformé pour obtenir la forme souhaitée. On peut emboutir une pièce plusieurs fois d’affilée pour lui donner sa forme progressivement.
L’emboutissage se combine souvent à une phase de pliage de la pièce et de découpe.
Les platines embouties sont souvent rivetées
En général, les deux faces d’une platine sont réalisées séparément. On les assemble ensuite à l’aide d’une pièce centrale sur laquelle les deux « lames » sont rivetées.
Un procédé moins onéreux
Ce procédé est utilisé sur la plupart des platines d’entrée et de milieu de gamme. Il est en effet moins coûteux que de l’extrusion par exemple : le fabricant perd moins de matière, il n’a pas non plus à fileter la platine pour accueillir des axes simples, contrairement à des modèles extrudés. De ce fait, les coûts de production sont réduits.
Les platines embouties offrent en général un meilleur rendement que des platines en composite de nylon et de fibre de verre, par exemple, mais se montrent limitées par rapport à des modèles extrudés ou taillés dans la masse, bien plus rigides.
Le moulage d’un châssis roller
Comme pour de nombreux autres métaux, il est possible de mouler l’aluminium. Il faut d’abord fabriquer le moule qui recevra l’aluminium en fusion. Une fois la pièce d’aluminium coulée et démoulée, un agent se charge de la finition. La photo ci-dessus montre l’un des derniers modèles de Powerslide réalisé par le biais de ce procédé, combiné avec une phase d’usinage et un bain d’anodisation.
La fabrication d’une platine extrudée
Les étapes de l’extrusion d’une platine
Le procédé d’extrusion est simple : Un bloc d’aluminium est mis sous pression puis contraint de traverser une filière (un orifice qui lui donnera sa forme). On obtient ainsi un profilé qui sera retravaillé pour atteindre la forme finale souhaitée par le fabricant. Cette technique donne une bonne rigidité aux platines. Cela ne peut se faire qu’avec un matériau présentation une certaine souplesse. Un matériau trop dur serait trop cassant.
Les platines usinées (taillées dans la masse)
Un châssis taillé dans la masse est en quelques sortes »sculpté » dans une pièce d’aluminium, comme le ferait un artiste dans du marbre. Là, on entre dans des productions en petite série et plutôt dans le très haut de gamme.
Le matériau utilisé est tellement rigide qu’il faudrait une presse d’une force considérable pour le plier. Ce procédé de fabrication permet de réaliser des choses impossibles à faire avec un profilé classique. Peu de fabricants emploient ce procédé de fabrication quasi artisanal. En France, ce sont les platines Diabolik qui sont réalisées grâce à ce procédé.
La finition des châssis en aluminium est un travail extrêmement minutieux. Tout est exécuté par machine numérique. Les découpes de platines sont peaufinées au laser. Il faut compter environ dix opérations pour achever une platine en aluminium.
Les marques ont ensuite tendance à apposer une sérigraphie sur les platines : soit par anodisation, comme nous l’avons vu, soit en ajoutant une simple couche de peinture.
![]() |
![]() |
La finition des platines en métal
L’anodisation : une option possible pour décorer et protéger
Les châssis de roller sont souvent anodisés pour accroître leur résistance à la corrosion. Il est aussi possible de les décorer en changeant la couleur des bains d’anodisation.
Le laser est souvent utilisé pour une meilleure découpe.
Liens utiles
Interview de Didier Chaplain, concepteur des platines Diabolik »
Anatomie d’une platine ou d’un châssis de roller
L’entretien du châssis ou platine de roller
Bien régler ses platines et châssis de roller
Bien choisir ses platines de vitesse (Par Yann Guyader, champion du Monde)
Roller course : quelle platine pour quel usage ?
Platines de vitesse : 2 ou 3 points ? Avantages et inconvénients…
Platines : magnésium ou aluminium ?
Photos : www.diabolik-skating.com
et Powerslide
rollerlife
18 juin 2015 at 11 h 00 minritaaaaz
14 mars 2013 at 20 h 00 minpro du foot
28 janvier 2010 at 20 h 44 minmama
27 mars 2009 at 14 h 50 minloli
5 février 2009 at 16 h 13 mincoucou
22 janvier 2009 at 16 h 18 min